Congratulation!!! St.Cera has its second factory put into production this May.
In 2019, St.Cera had its wholly-owned subsidiary in Pingjiang High-tech Area, Hunan Province. It covers an area of about 30 acres with construction area of about 25,000 square meters.
Possessed with advanced technologies of the full procedure of precision ceramic parts fabrication, such as ceramic powder treatment, Dry Pressing, Cold Isostatic Pressing, Sintering, Internal and Cylindrical Grinding and Polishing, Plane Lapping and Polishing, CNC machining, St.Cera is able to manufacture precision ceramic components with various shape and accuracy. To ensure the final product with no defect, it has to pass the test by precision testing instruments before delivery.
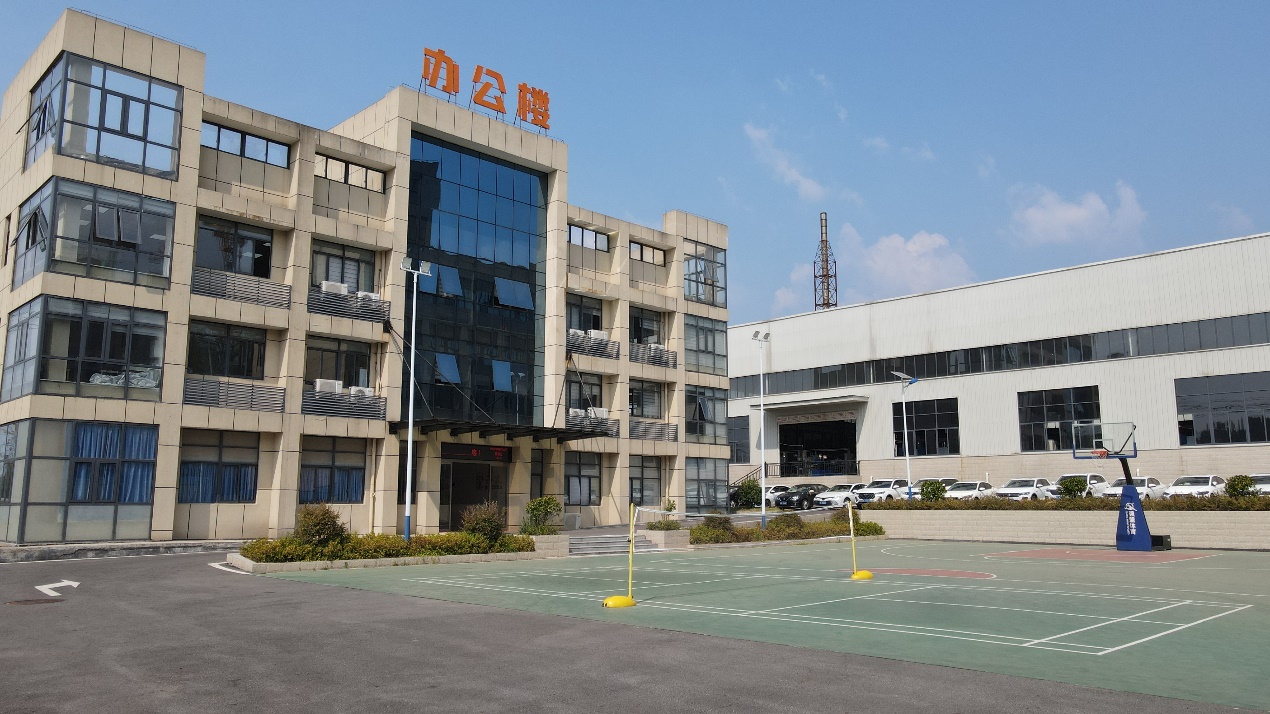
In addition, St.Cera has different kinds of dry pressing equipment (5T, 25T, 125T, 1250T), which could produce all sizes of products. We have the biggest cold isostatic pressing equipment of ø800X2000mm, which could produce parts in large size; as well as many large sintering furnaces, which could produce high-quality and high purity ceramic raw materials under precision temperature control.
St.Cera has applied ISO 9001 and ISO 14001 standard on cleaning technology. ISO Class 6 cleanroom and various precision inspection equipment, which can meet the cleaning, inspection and packaging requirements of high-end ceramic parts.
With the goal of being the precision ceramic parts manufacturing specialist, St.Cera adheres to the business philosophy of good faith management, customer satisfaction, people-oriented, sustainable development, and strives to become a world first-class precision ceramic manufacturing enterprise.
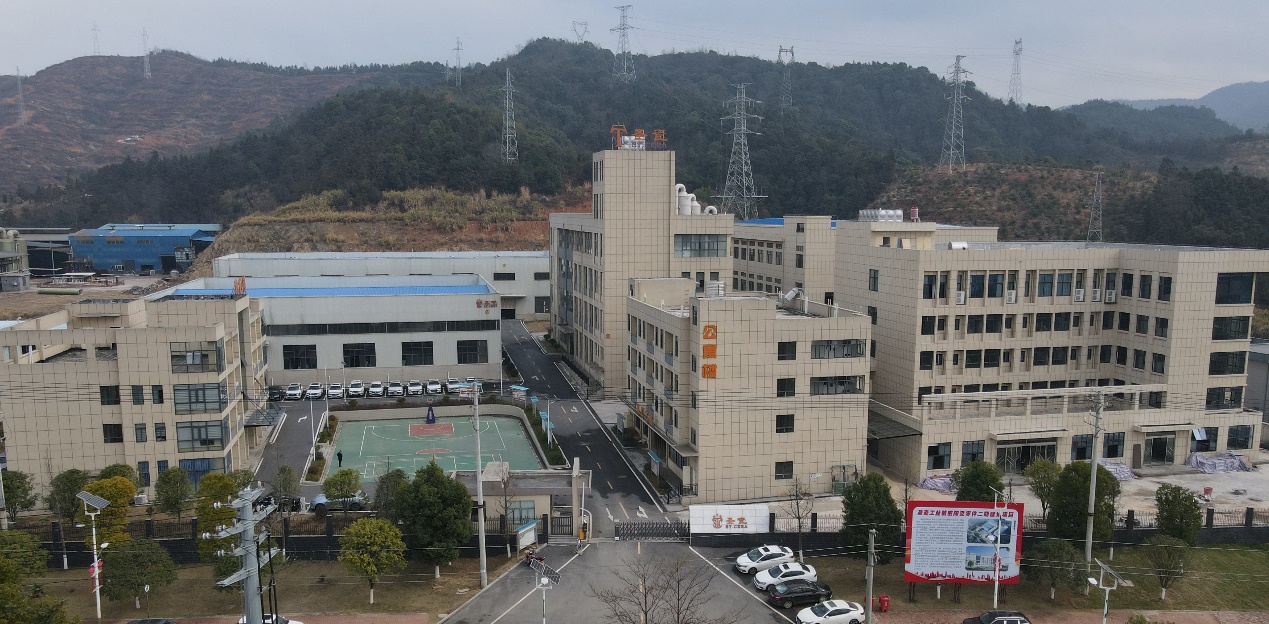
Our main product are ceramic end effector and semiconductor equipment ceramic spare parts. With features of high temperature resistance, corrosion resistance, abrasion resistance and insulation, ceramic end effector can work in most kinds of semiconductor equipment for a long time, which has conditions of high temperature, vacuum or corrosive gas. It is made of high-purity alumina powder, and processed by cold isostatic pressing, high temperature sintering and precision finishing. The dimension tolerance can reach to ±0.001mm, surface finish Ra0.1, and maximum working temperature up to 1600℃. With our unique ceramic bonding technology, the ceramic end effector with vacuum cavity can work in a high temperature up to 800℃. Be made of high-purity (above 99.5%) alumina ceramic, formed by cold isostatic pressing and sintered under high temperature, then precision machined and polished, the ceramic spare parts can meet any strict requirements of semiconductor equipment with its features of wear resistance, corrosion resistance, low thermal expansion, and insulation.
Based on the increased production capacity, welcome companies in Semiconductor, New Energy, Automotive and other fields contact us for business cooperation.
Post time: May-03-2021